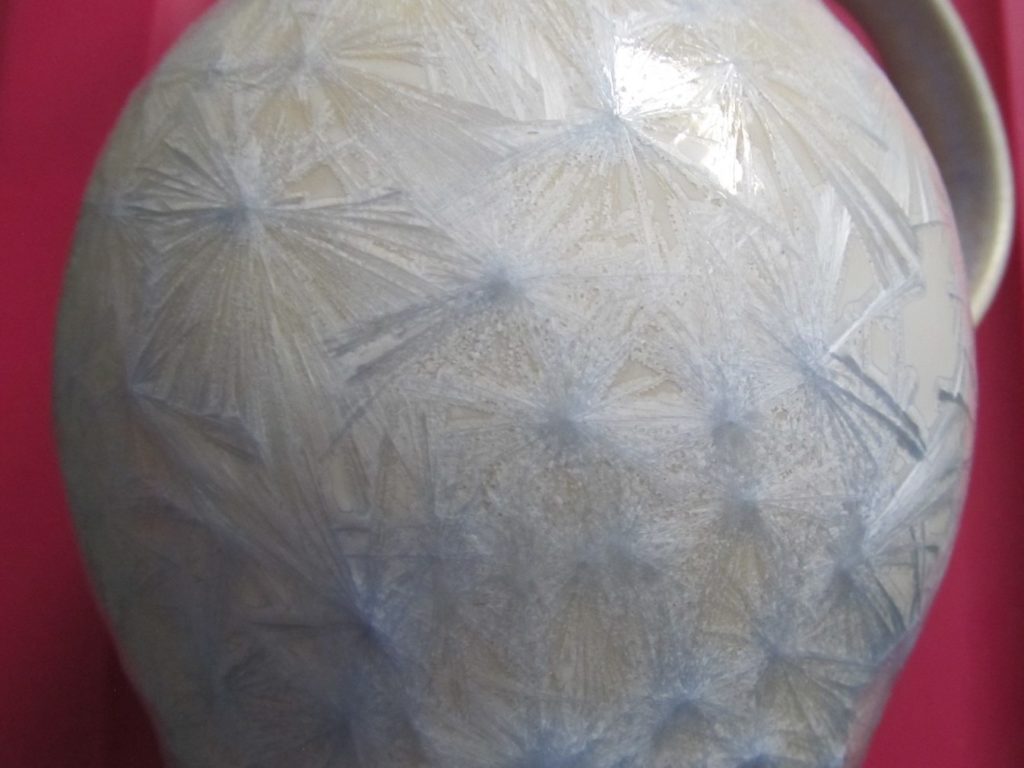
People have used crystalline glazes to decorate their pots with many different glaze recipes throughout the years. Adelaide Alsop Robineau who lived from 1865 to 1925 used some crystalline glazes. A blog entry on the ‘Home’ page, titled ‘An Interesting Figure in Ceramic History’ tells more about her.
The firing process for pots glazed with crystalline glazes is very often different than that needed for regularly glazed pots. There is a longer soak time built in to the firing that gives the crystals time to grow while the glaze is molten. A soak time is where the kiln temperature is held at the same temperature for a certain period of time. To give the crystals more time to grow, a down ramp is also used. That means that enough heat is still applied after the kiln has reached its highest temperature so that the kiln cools down at a slower rate than it would if it was allowed to cool down naturally.
Usually there are two firings for a piece of pottery. The first firing comes after your clay items are completely dry, which is termed bone dry. It is called a bisque firing. The bisque firing removes all the water from your pots, and is usually fired to what is called a cone temperature of 06 or 08. Which is around 1828 degrees Fahrenheit to around 1728 F. You read that right, if there is a zero before the number, the larger looking number is actually cooler in temperature. In other words, cone 08 is around 1728 F and cone 06 is hotter at around 1828 F degrees.
You do not have to worry about that with most glaze firings since they do not often have zeros in front of their numbers. Cone 6, for instance is around 2232. Some glaze firings are only to cone 5 at 2167 or cone 6 and are done with an electric kiln. The glaze firings that a large gas kiln can handle, however, go up to cone 9 at around 2300 F and cone 10 at around 2345 F.
The glaze is applied to the pots in a liquid or aerosol form. Most often the pots are dipped in a glaze bucket, then their bottoms are wiped off with a small sponge. Often potters use an aid to washing them off called wax resist, which is applied before glazing, and it helps prevent glaze from spilling onto the kiln shelf. Then the glaze is left to dry before this second firing. One of the reasons glazing that way works is because the bisque-ware is somewhat porous, so the liquid glaze sticks to the pots. The temperatures are measured by cones because Josiah Wedgwood invented what are called pyrometric cones. Those are cones that start out as small, solid, triangular posts. As a kiln reaches a certain temperature, each cone, which is inserted in a row in a glob of clay, melts and bends to fall over. This helps the person running the firing to monitor the clay temperature.
Along with a difference in glaze kiln firing rates, most crystalline glazes are more runny than most regular glazes and are very likely to stick to the kiln shelves. To compensate for this, bisque fired saucers are placed on the kiln shelf under pieces with crystalline glazes on them. If the glaze travels onto the saucer, it will stick the two objects together (better them than the kiln shelf). Most times, the saucer can be carefully broken free from the originally glazed piece, and the glaze that ran, will be jagged and sharp. The glaze then needs to be ground down with a grinding stone so the piece can be safely used.
For more information on crystalline glaze firing, check out this article at The Spruce Crafts: